Inside the Cybertruck’s Bold Electronics Revolution
Tesla’s Next-Gen Secrets: In this continuation of our exploration into Tesla’s technology, we deep-dive into the bold leaps Tesla is making with the Cybertruck (or Post Cybertruck E/E architecture)
We are exploring Cybertruck—from the monumental 48V system to the revolutionary EtherLoop network. Buckle up for an electrifying journey through Tesla’s tight hardware-software integration, and discover why the rest of the industry might want to take notes.
1. Introduction
Earlier, we asked the all-important question posed by Sandy Munro—“Why isn’t Tesla selling its software stack to other OEMs?” The short answer: Tesla’s software is so tightly integrated with its own hardware ecosystem that splitting them apart would be like trying to surgically remove a car’s brain and transplant it into a different body. It’s not just about code; it’s about the holistic synergy of sensors, controllers, networks, and even developer tools that Tesla has built from scratch.
Tesla’s dedication to vertical integration means every bolt, wire, chip, and line of code is optimized to work together in harmony. By keeping software development in-house, Tesla ensures:
Faster iteration and feature rollout.
Seamless Over-The-Air (OTA) updates.
A consistent, Tesla-first user experience.
In other words, offering Tesla’s cutting-edge software to another OEM might be as jarring as playing a Nintendo cartridge on an Xbox—fascinating in theory, but nearly impossible in practice.
2. What Has Changed from Pre-Cybertruck to Cybertruck?
From its early Model S and Model X days to the futuristic Cybertruck, Tesla has hinted at or directly revealed significant upgrades to its electronics architecture. Here are some of the big ones:
48V Architecture – Moving away from traditional 12V to a more robust 48V system. (Widely discussed at Investor Day.)
EtherLoop – A unique twist on automotive Ethernet, aiming for high-speed, low-latency communication.
Wiring System Upgrades – Fewer, thinner, and more efficient wires.
Zonal Architecture – Localizing electronic control to different “zones” of the vehicle.
85% In-House Controllers – Eliminating third-party dependencies, maximizing synergy.
These changes serve as the technological backbone of the Cybertruck, ensuring it’s as durable inside as it appears on the outside. While final production details may vary, Tesla’s overall direction is consistently moving towards tighter hardware-software integration and more efficient electrical systems.
3. Let’s Deep Dive into Each Topic
3.1. The 48V System: A Powerhouse Upgrade
Why 48V?
Reduced Current, Less Heat: Higher voltage means lower current for the same power, lowering heat generation and the risk of wire meltdown (not a fun scenario!).
Better Efficiency & Weight Savings: Thinner wires can carry the same power, cutting down on weight and boosting range.
Future-Proof for High-Power Demands: Think advanced computing systems, smart sensors, or possibly other high-power accessories Tesla might integrate.
Trivia: Going from 12V to 48V is like switching from a foot pump to an electric air compressor. Both accomplish the same task, but one does it way faster and more efficiently.
3.2. EtherLoop: The Next Generation of In-Car Communication
What Is EtherLoop?
“EtherLoop” is a term being used by the EV community (including teardown experts like Sandy Munro) to describe Tesla’s evolving automotive Ethernet approach. Traditional automotive communication buses (like CAN) are robust but can be bandwidth-limited. By leveraging an Ethernet-based solution, Tesla aims for higher data throughput and lower latency.
Key Advantages
High Bandwidth & Real-Time Data: Autopilot systems, cameras, and sensors can transmit and receive large volumes of data without major bottlenecks.
Reduced Latency: Crucial for active safety features and real-time sensor fusion.
Improved Debug-Ability: EtherLoop allows deeper diagnostics and faster fault isolation through the single interface. This makes software iteration and real-time troubleshooting much more efficient. Conventionally we need to connect different interfaces (different CAN buses) & time-sync data outside.
Active Road-Noise Cancellation on EtherLoop—What’s the Big Deal?
Picture this: in-cabin noise data from multiple sensors and microphones is captured, then instantaneously sent to a central processor to generate “anti-noise” signals. That information has to loop back to the speakers or actuators just as quickly—all in real time. By leveraging EtherLoop’s high-speed, bi-directional automotive Ethernet design, Tesla can achieve the bandwidth and redundancy needed to ensure data zips back and forth without delays or choke points.
In contrast, traditional automotive buses often lack the speed or capacity for such rapid data exchange, forcing automakers to use specialized hardware (like serializers and deserializers). This not only adds cost and complexity, but also creates more potential failure points. With EtherLoop, Tesla integrates Audio routing directly into its core network architecture, minimizing hardware overhead and delivering a more robust, future-proof solution.
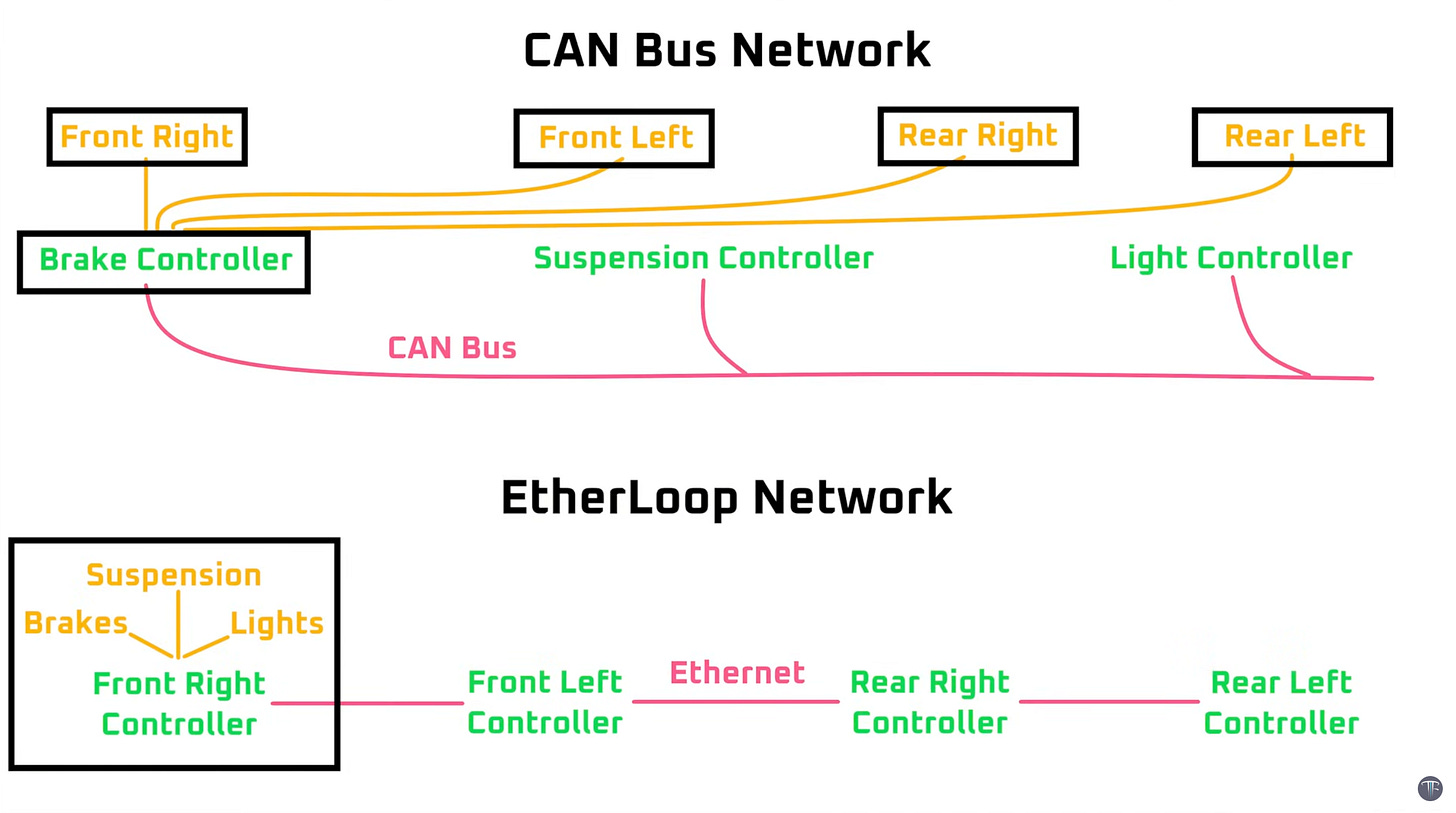
Trivia: Think of a typical automotive data bus like you and your friend talking through paper cups connected by string; EtherLoop is more like FaceTiming on 5G—snappy, flexible, and built for modern demands.
3.3. Wiring System Upgrades
Gone are the days of bulky wiring harnesses snaking around like spaghetti. With a zonal architecture and a 48V backbone, Tesla is expected to reduce wiring length, saving both weight and manufacturing complexity. Each zone of the vehicle (front, mid, rear) would have localized control modules that communicate via EtherLoop, reducing both the thickness and the quantity of wires required.
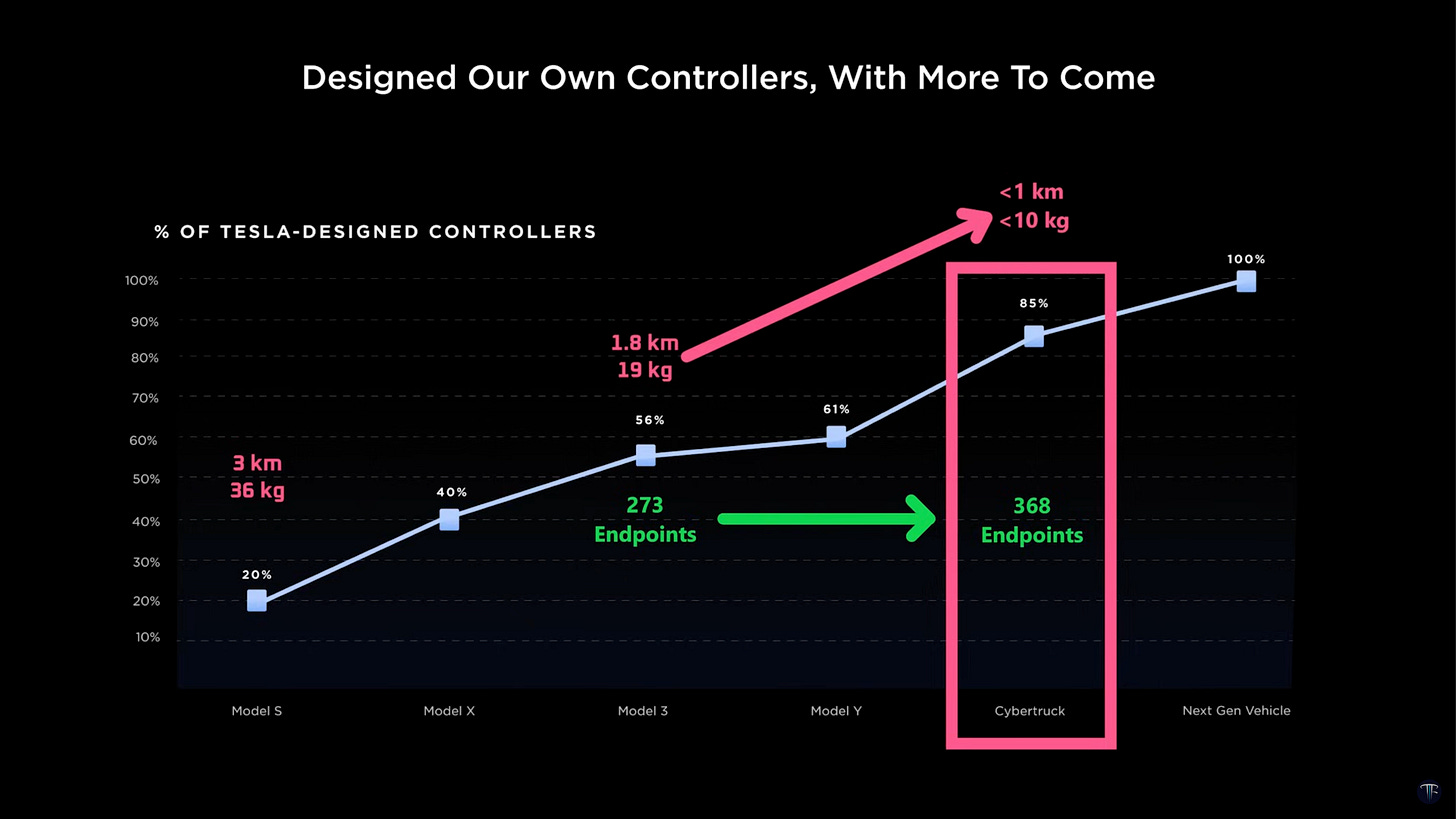
3.4. Zonal Architecture
Why Zonal?
Modularity: Upgrades become simpler. Need to swap a sensor in the front zone? Replace just that module or harness.
Reduced Latency: Data doesn’t have to travel back and forth across the entire car.
Tesla’s approach to zonal architecture streamlines both production and service. It reduces potential failure points, simplifies diagnostics, and can speed up the manufacturing process by assembling the car in distinct “zonal” phases.
3.5. 85% In-House Controllers
If you can own your supply chain, you can own your destiny. By bringing nearly all controllers in-house, Tesla eliminates the typical back-and-forth with external suppliers. This close integration means:
Over-the-air updates for everything: From your infotainment system to your seat control modules.
Faster innovation cycles: There’s no middleman in the feedback loop.
Uniform software style: Across all controllers, reducing software bloat and anomalies.
4. Conclusion: The Vertical Integration Masterstroke
The Cybertruck is more than just a rolling slab of stainless steel; it’s a testament to how deeply Tesla integrates its hardware and software. By overhauling the electric system to 48V, introducing the EtherLoop network, and consolidating control under a zonal architecture, Tesla continues to tighten its hold over every facet of the automotive experience.
It’s not that Tesla won’t sell its software to other OEMs—it’s that no other OEM’s hardware is truly prepared for Tesla’s level of integration. It’s akin to trying to run macOS seamlessly on a random PC—it might be theoretically possible but requires an immense amount of custom engineering to make it work flawlessly.
Meanwhile, Tesla’s “software first” philosophy shapes both the product and the ecosystem it is building. From developer tools to over-the-air updates, the entire platform is treated like a living, updatable computer system on wheels. In future blogs, we’ll delve deeper into Software-first, platform and ecosystem approach—so stay tuned!
5. Learnings for Legacy OEMs
Prioritize In-House Development: Controlling core systems often yields better agility and innovation.
Focus on Synergy: Hardware-software integration ensures a cohesive user experience and faster deployment of new features.
Embrace Modular Zonal Designs: Easier maintenance, fewer parts, simpler manufacturing.
Adopt a Software-First Mindset: By building a robust ecosystem, OEMs can keep vehicles future-ready and competitive.
Streamline Wiring: A higher voltage system and a more centralized network can help eliminate “spaghetti wiring.”
If traditional carmakers take these strategies to heart, they may keep up with Tesla—without feeling like they’re constantly in catch-up mode.
6. References & Further Reading
Digging Deeper on Tesla's Etherloop Wiring System by The Limiting Factor: In-Depth Look at Automotive Architecture (YouTube)
Tesla Cybertruck DEEP DIVE with 5 Tesla Executives! by Munro Live: Tesla’s Electronics Evolution (YouTube)
Tesla Investor Day 2023 – Event Recording & Slides
IEEE Spectrum on Automotive Ethernet – “Automotive Ethernet: The Road to Fast, Secure In-Car Networks”
Original Post Inspiration – Inside Tesla’s Brain: Before Cybertruck
Disclaimer: Specific technical details like “EtherLoop” naming, “85% in-house controllers,” and the exact 48V implementation come from Tesla investor presentations, industry teardown analyses, and public speculation. Tesla’s final production versions may have variations.
This blog is edited and enhanced with ChatGPT o1
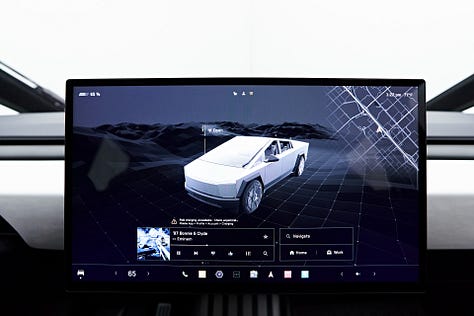
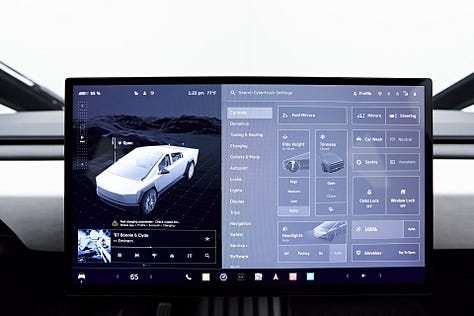
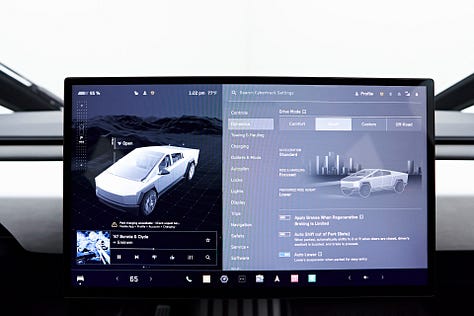
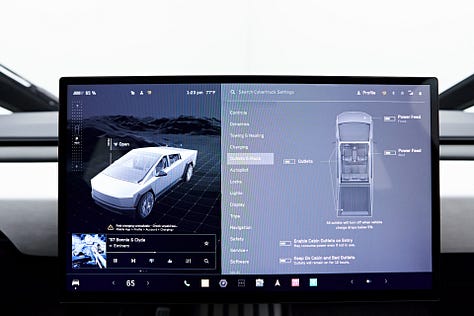
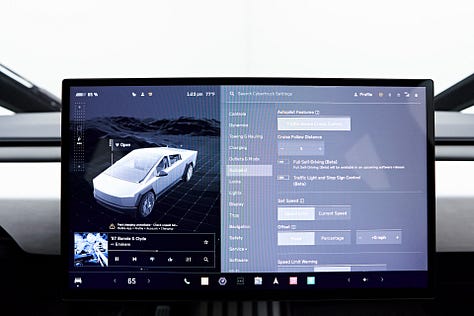
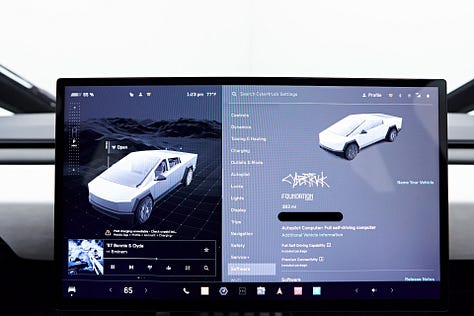
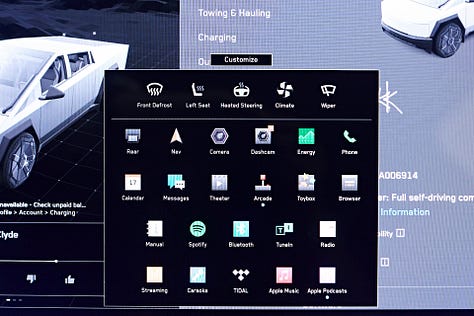

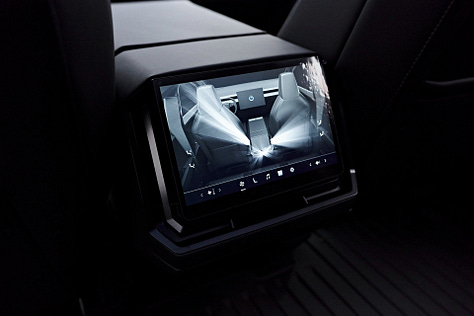