Reality of Rivian R2: Setting Industry's SDV Benchmark
Rivian’s R2 platform is poised to be a SDV exemplar, showcasing a groundbreaking electrical/electronic (E/E) architecture. By moving to a zonal architecture and consolidating computing.
1. Introduction
The Rivian R2 platform is more than just another electric vehicle—it represents a fundamental shift toward true Software‑Defined Vehicles (SDVs). By rethinking the electrical/electronic (E/E) architecture from the ground up, consolidating compute into a handful of powerful nodes, and placing software at the centre of vehicle design, Rivian has achieved dramatic reductions in complexity, cost, and weight, while enabling continuous over‑the‑air (OTA) innovation. In this blog, we explore the key pillars of R2’s Gen 2 architecture: its zonal ECU layout; the software abstractions that make it work; the tangible cost and weight savings; and how Volkswagen’s strategic partnership validates this approach.
Rivan R2 is introduced with their Gen2 E/E Architecture. In this blog, R2 & Gen2 are used in a similar meaning.
2. Superior Software‑Defined Vehicle
Rivian’s R2 embodies the SDV ideal: software is the primary vehicle differentiator, and the hardware is merely a flexible execution layer. By consolidating functions onto powerful zonal and central controllers, Rivian can push focused OTA updates without new physical modules—streamlining feature rollouts and bug fixes alike.
Video demonstrating Software Release and Feature updates. (Source: rivian.com)
Software‑First Philosophy
Features delivered via OTA updates, with hardware engineered to support growing software demands
Modular software layers enable rapid addition of new capabilities (e.g., camping mode, pet comfort)
High‑Performance, Centralized Compute
Seven ECUs (down from 17 in Gen 1 vehicles and ~40–150 in legacy cars)
Shared hardware resources allow multiple functions to run on the same node
Vertical Integration & Agility
In‑house hardware and software development, mirroring Tesla’s strategy
Gen 1→Gen 2 migration completed in ~2 years on the same software stack
3. Gen 2 E/E Architecture
3.1. Overview
By moving to a zonal layout, Rivian drastically simplifies the vehicle’s wiring harness and provides a data-centre-like network fabric under the skin. Each zone controller is a general‑purpose computer managing all devices in its region, while four central ECUs handle high‑level domains: autonomy, infotainment, vehicle access, and powertrain.
Zonal vs. Domain‑Based
Domain‑based (Gen 1, many legacy vehicles): ECUs grouped by function (e.g., body, chassis, infotainment)
Zonal (Gen 2 R2): ECUs organized by location—West (left), East (right), South (rear)—plus four central units
Ethernet‑Centric Network
Replaced ≈1.6 miles of copper wiring with multi‑gigabit Automotive Ethernet
Unified in‑vehicle LAN carries sensor data, commands, and diagnostics in real time
Scalable, Modular Topology
New sensors or actuators plug into a zone and join the network, no dedicated ECU required
3.2. Zonal ECU Design: Engineering Simplicity
Rivian collapsed dozens of dedicated modules—window motors, mirror controllers, lighting modules, door ECUs—into just three zonal controllers. This clean‑sheet design not only slashed material and labour costs but also improved reliability (fewer connectors to corrode or break) and serviceability (faults are confined to one zone rather than a mile‑long harness).
Table 1. “Magnificent Seven” ECUs
Consolidation Benefits
Removed ~500 parts (ECUs, connectors, harness segments)
Cut ≈44 lbs of wiring and harness weight
Eliminated physical fuses in favour of MOSFET‑based “virtual fuses”
Streamlined Assembly
Fewer harness variants, more factory automation
Reduced assembly time and error points
Reliability & Serviceability
Shorter, simpler wiring reduces failure opportunities
Zone ECUs localize faults, speeding diagnostics
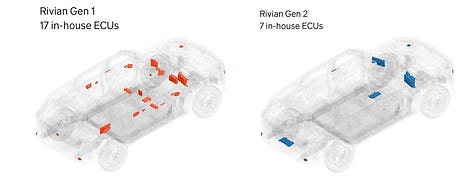
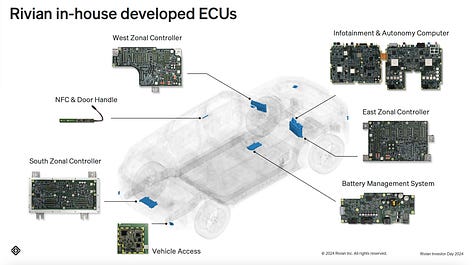
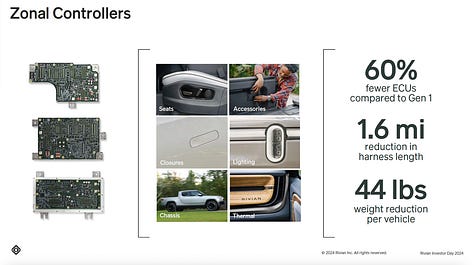
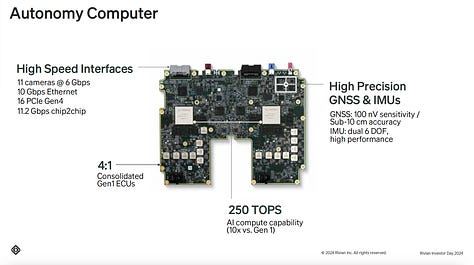
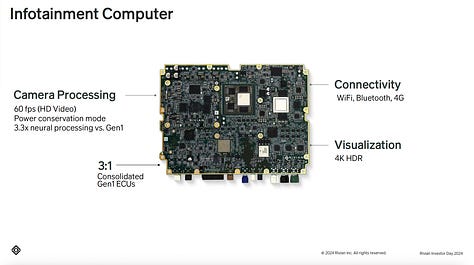
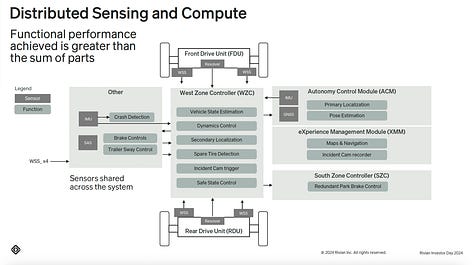
4. Software: Managing and Abstracting Complexity
Rivian’s software is the “central nervous system” knitting together the simplified hardware. By rewriting and optimising code for zonal consolidation, rather than porting legacy supplier stacks—they achieved a lean, cohesive platform. Event choreography (e.g., emergency braking sequence) is handled seamlessly over the Ethernet backbone, with each ECU executing its piece in milliseconds.
Unified Software Platform
End‑to‑end in‑house stack, from firmware to cloud APIs
Shared services (e.g., window control, lighting service) across ECUs
Service‑Oriented Architecture
Abstracts hardware details, enabling high‑level features to orchestrate multiple zones
Facilitates coordinated behaviours (e.g., AEB triggers lights, seatbelts, screens)
OS Diversity for Fit‑for‑Purpose
Linux/Android for infotainment and autonomy nodes
RTOS/AUTOSAR for zonal and powertrain ECUS with real‑time constraints
5. Rivian Gen2 vs. Legacy Architectures
The leap in consolidation is staggering: compared to a typical premium sedan with dozens of ECUs, R2’s seven controllers manage every function from propulsion to infotainment. Shorter, simpler wiring not only cuts weight but also reduces hand‑built harness complexity—a major bottleneck for traditional OEMs.
ECU Count: 7 (R2) vs. 17 (Gen 1) vs. 40–150 (legacy)
Wiring Harness: 1.6 miles removed in R2, enabling lighter, more reliable builds
Factory Automation: Simplified harnesses allow for greater use of robotics and faster assembly
Fragmentation: Legacy cars often have siloed subsystems—R2 offers a unified experience
6. E/E Driven Cost Efficiencies of Gen 2
By trading many low‑end ECUs for a handful of powerful ones, Rivian capitalised on chip-economies of scale. Eliminating physical fuses, multiple harness variants, and redundant modules yielded thousands of dollars in per‑vehicle savings, crucial for hitting a ~$45k R2 starting price while
Production Savings: ≈20% lower electronics BOM cost
Material Cost: ≈35% reduction in wiring/electronics assembly costs
Weight Reduction: ~20kg saved, translating to range or battery‑pack savings
Software Economics: One platform vs. many codebases—fewer engineering hours and warranty claims.
7. Conclusion
Rivian R2’s Gen 2 architecture is a blueprint for the next generation of vehicles: minimal hardware footprint, maximal software flexibility, and a network‑centric design that fosters continuous innovation. By consolidating dozens of modules into seven versatile ECUs and embedding a unified software platform, Rivian achieved unparalleled cost, weight, and complexity reductions—earning industry validation from partners like Volkswagen. As automakers worldwide embrace SDVs, Rivian’s R2 stands out as the new reference design for how to build truly software‑driven, future‑ready vehicles.
References
Rivian 2024 Investor Day Presentation Slides. Link
InsideEVs, Why ‘Zonal Architectures’ Are The Next Big Thing In EV Design, 2024. Link
Fast Company, The Rivian R1 is getting a major under‑the‑hood redesign, 2024. Link
Popular Science, How Rivian reduced electrical wiring by 1.6 miles and 44 pounds, 2024. Link
Design News, New Tech, Longer Range, and Lower Prices Keep Rivian in the Game, 2024. Link
Charged EVs, At Rivian’s Electrical Hardware Lab, Sandy Munro checks out the new GEN2 architecture, 2024. Link
Counterpoint Research, Volkswagen Invests $5 Billion in Rivian, Forms Joint Venture, 2024.Link
S&P Global Mobility, BriefCASE: Legacy to leapfrog? How the Rivian deal propels Volkswagen forward in the SDV race, 2024.Link
This blog is edited and enhanced with Chatgpt o4-mini & Research supported by Chatgpt o3